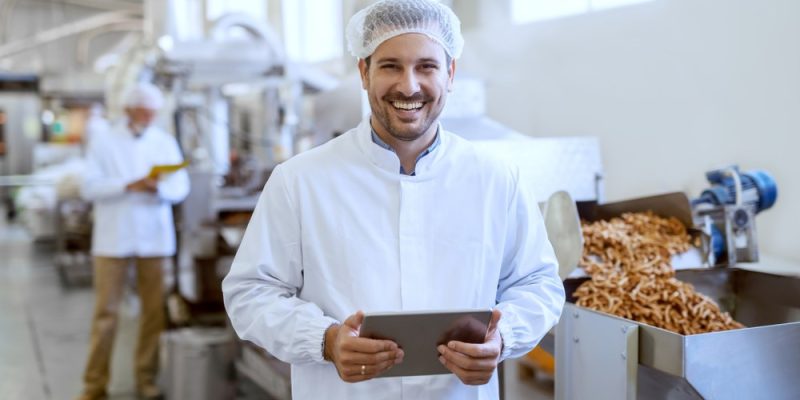
Revolutionizing Food Processing with Artificial Intelligence
The manufacturing process, especially in the food and beverage industry, presents a variety of uncertainties. It can be difficult to identify the factors that cause failures and determine what constitutes a good product or when to discard it. However, processing equipment may hold the answers to these questions.
Artificial intelligence (AI) and machine learning provide a means for processing equipment to handle complexities and causations that are too intricate or numerous for the human mind. AI is already being applied in some food processing applications and has the potential to revolutionize other areas, including maintenance, sanitation, and logistics.
According to Richard Phillips, Director of Smart Manufacturing at Polytron, a member of the Control System Integrators Association, “AI and machine learning will impact most areas of manufacturing and the supply chain in some way. We are already using predictive maintenance and analytics, as well as schedule optimization, in the food and beverage industry.”
Improving Product Quality with Artificial Intelligence
Artificial intelligence (AI) has become a popular tool for sorting, grading, and inspecting both ingredients and finished products. AI can aid in two ways: by establishing standards and specifications, and by assisting in determining the cause if a product deviates significantly from its specifications.
Key Technology, a supplier of sorting systems, initiates most applications with a “sort recipe” of the expected appearance of the product, according to Marco Azzaretti, the director of marketing. However, the end product is always a customized sorter, programmed for the unique processing line on which it will be installed, as each installation has its unique definitions of acceptable in-spec products, as well as the precise flaws, foreign materials, and contaminants that must be removed.
The Key system utilizes visual inspection in regular light. However, other types of inspections can also benefit from AI. ImagoAI, for example, employs hyperspectral imaging with AI to inspect components like fat and protein, detect toxins, and more, replacing traditional methods of detection like near infrared.
“Imaging with AI provides higher accuracy and lower detection limits,” says Abhishek Goyal, the CEO and co-founder of ImagoAI. “Companies are increasingly concentrating on applications that utilize imaging AI to attain lower detection limits or address more complex physical relationships.”
Like near infrared, ImagoAI requires 50 to 100 samples to establish inspection standards. However, ImagoAI can process images remotely and transmit the results to the equipment, allowing its customers to take advantage of AI modeling technology without being experts in the field.
Read Also:
- AI in Food and Beverage Industry: Use Cases & Benefits
- AI in Food Packaging: Smart Solution for the Future
- How Does AI Impact Food Delivery?
Prediction vs. Prevention
AI has the potential to revolutionize maintenance strategies by shifting from preventive to predictive maintenance. The former relies on fixed schedules to service or replace equipment, whereas the latter continuously monitors equipment and analyzes its performance to predict when attention is required.
Through continuous monitoring of equipment parameters such as temperature and vibration, AI develops a performance profile that indicates when equipment needs replacement. This is done by attaching sensors to equipment such as motors and gearboxes that continuously feed back data to a cloud-based AI application, which analyzes it to identify patterns and develop maintenance schedules.
However, implementing a preventive maintenance program is not a simple task, especially for parameters like vibration, which is subject to many external variables. David McKenna, the director of smart manufacturing solutions at Grantek Systems Integration Ltd., is skeptical about its potential effectiveness due to the unpredictable nature of equipment failures.
According to McKenna, even with the use of sensors, finding patterns in random and inconsistent equipment failures is difficult. He believes that preventative maintenance will not eliminate a significant amount of downtime.
Identifying the Causes
When it comes to resolving issues such as downtime or out-of-spec products, artificial intelligence (AI) has the potential to examine a more extensive range of factors and potential causes than the human mind. By detecting variations in inputs and other factors, AI can identify correlations that might go unnoticed by human observers.
Liran Akavia, co-founder of Seebo, an AI software provider, explains that any production line can have different losses and inefficiencies, even for different products produced on the same line. These losses can result from various factors such as waste due to overweight, quality rejects, size and shape variances, color inconsistencies, unstable yield, among others. The root causes of these losses also vary from one production line to another.
Recently, a bakery in Europe faced a persistent underweight product issue, which Seebo’s software helped to resolve. The software successfully identified two parameters that consistently correlated with underweight products: a baking temperature above 400°F and a conveyor belt speed of less than 5 meters per second. After adjusting these factors, the underweight products decreased from 7.4% to 2.2% of production, leading to an annual saving of approximately $1 million.
To get to the root of the problem, Seebo had to consider many other factors beyond just the temperature and bake time, according to Akavia. The Seebo solution continuously conducts multivariate analysis on all the data relevant to the production process, including raw material data, quality data, external data such as weather, temperature, or humidity. Literally, every relevant piece of data is analyzed 24/7, including the complex and dynamic interrelationships between different data tags on the production line.
Revolutionizing Equipment Sanitation with Artificial Intelligence
As technology advances, we continue to discover new ways to improve our lives. One such area is the use of artificial intelligence (AI) in equipment sanitation. Clean-in-place (CIP) is a widely used method for cleaning equipment, but it consumes vast amounts of water. To address this issue, researchers at Nottingham University in England are developing a system that incorporates AI technology to minimize water usage.
The system utilizes ultrasound and ultraviolet sensors to provide feedback and monitor fouling on equipment and pipework. Ultrasonic sensors are attached to the outside of the equipment, while the UV system is placed inside the top of a tank, featuring UV lights and a camera. With the use of machine learning models, the sensors detect and determine when all the fouling has been removed.
Nicholas Watson, an associate professor of chemical engineering at Nottingham University, explains, “The model, as it now stands, is intended to minimize water use. Other models could be developed to optimize parameters such as flow rates, temperature, and chemical concentration to reduce time and resource use, linked to environmental sustainability, but this is the next stage of our work.”
The integration of AI and machine learning models in sanitation processes can revolutionize efficiency and sustainability in food production. The technology can be applied judiciously to address some of the most challenging sanitation applications.